Your requirement. Our solution.
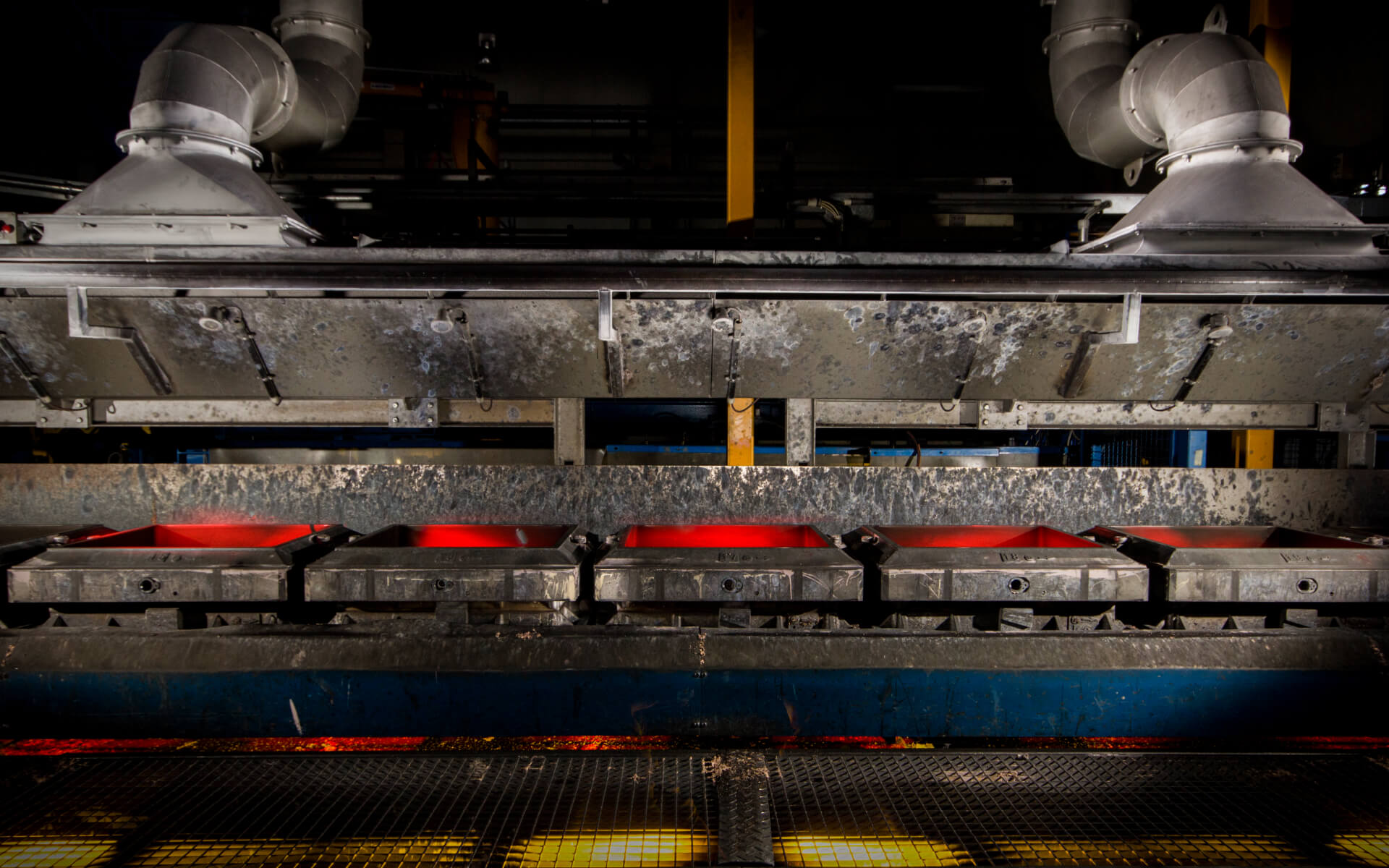
Sand casting process for both series and single parts
We rely on the sand casting process in our in-house foundry. As a traditional casting technology, sand casting allows us to cast both series and individual parts in a proven and economical manner. The sand casting process is a casting technique that uses molds - as the name suggests - made of sand. After casting, the sand is recycled in our foundry and can be processed into new molds - entirely in the spirit of a resource-saving circular economy.
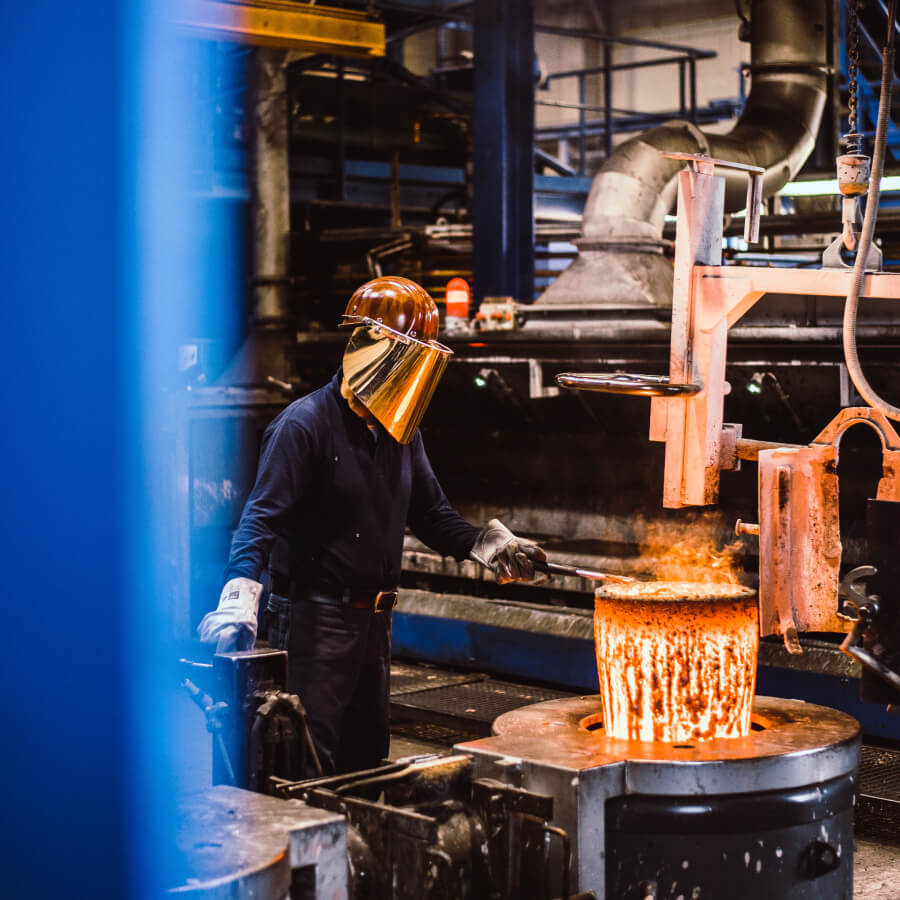
Sand cores for cavities and complex geometries
If a casting needs to have a cavity on the inside or if it needs to have complex geometries, so-called cores are used. These are bodies of compressed sand which are inserted into the mold at designated points and which fill the later required cavity. We take over the core production for you as a service.
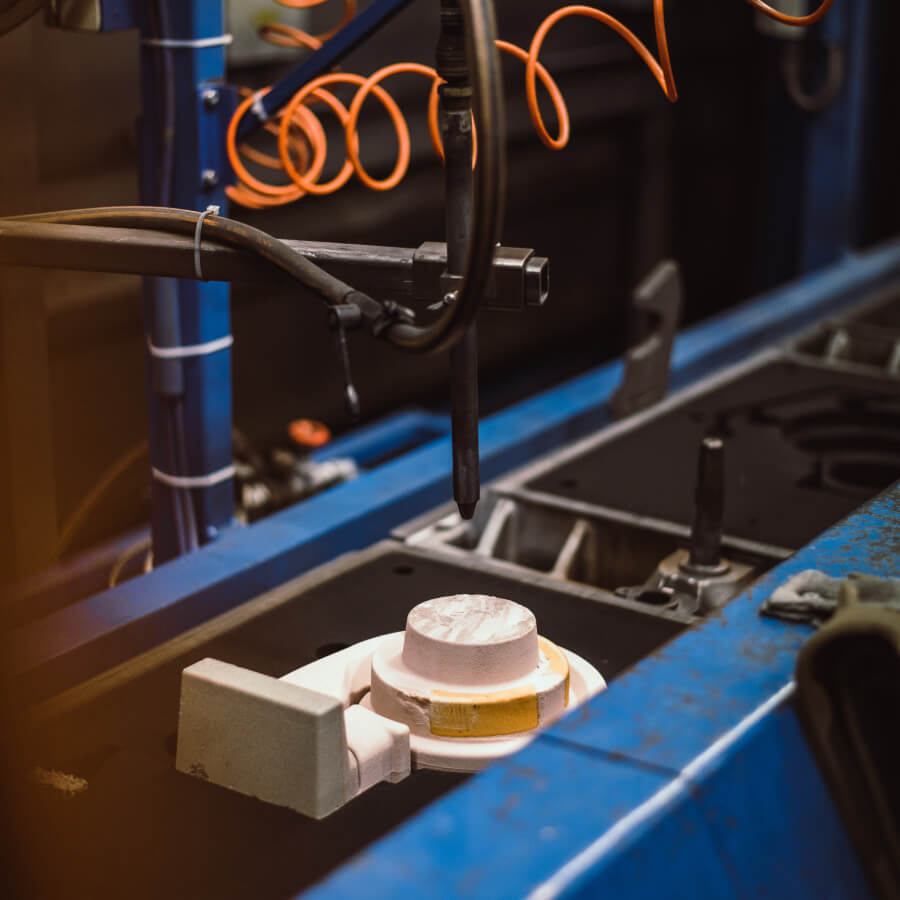
Molding on the automatic molding line
The mold boxes are put together on our automatic molding line (HWS). Our box size is maximum 650 x 450 x 200/200 mm. After merging the casting process takes place. We cast the desired alloys using up to four induction furnaces with a volume of 150 or 100 kg per crucible. Depending on the casting, we automatically form 50 to 60 boxes per hour. Sand casting works on the principle of the lost mold. This means that the sand mold is destroyed after being used once.
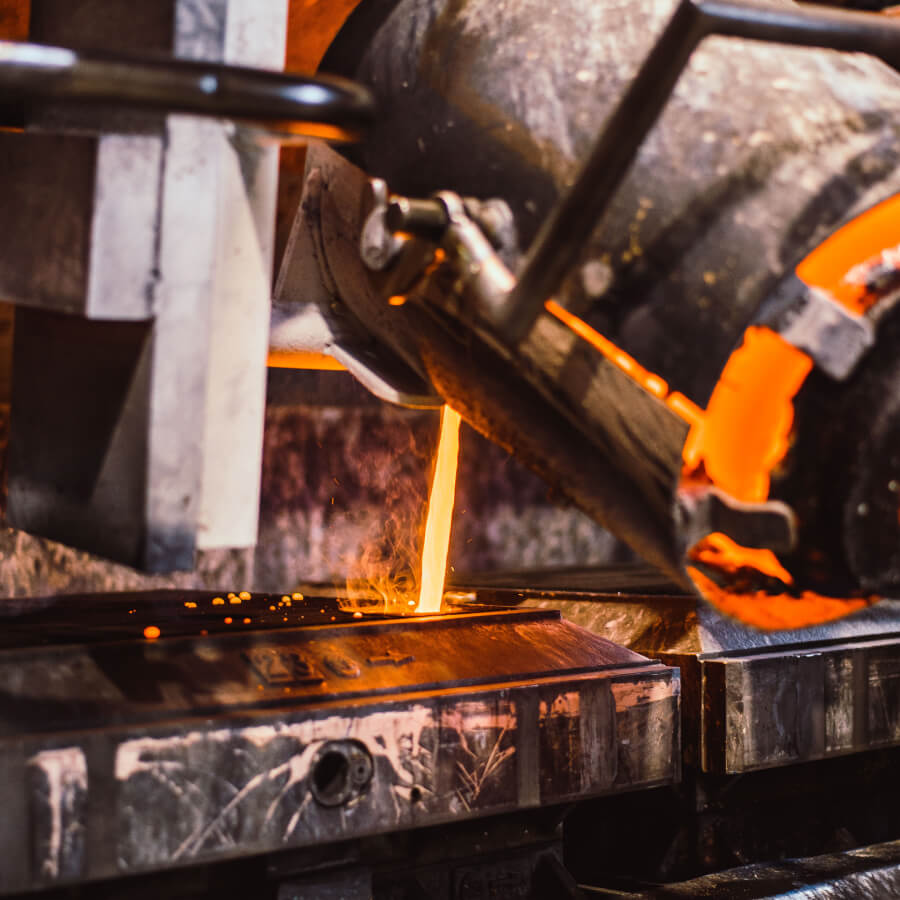
Casting as unmachined part or mechanically processed
Following the casting, we rely on an internal finishing department in our foundry. Here, the castings are separated if necessary, the sprue is ground off and the unfinished parts are blasted and cleaned. We also use cleaning robots for this purpose. The separated materials can be remelted as recycled material. The castings can either be delivered as unfinished parts or further processed by our mechanical processing department.
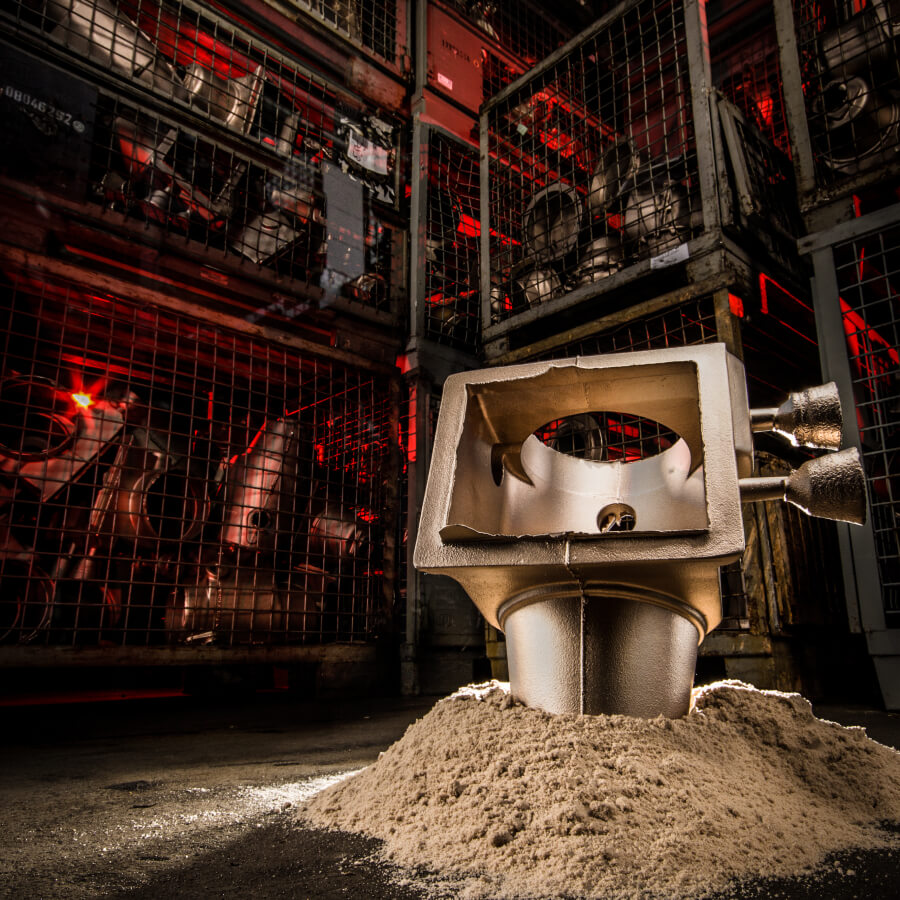